КАТЕГОРИИ:
АстрономияБиологияГеографияДругие языкиДругоеИнформатикаИсторияКультураЛитератураЛогикаМатематикаМедицинаМеханикаОбразованиеОхрана трудаПедагогикаПолитикаПравоПсихологияРиторикаСоциологияСпортСтроительствоТехнологияФизикаФилософияФинансыХимияЧерчениеЭкологияЭкономикаЭлектроника
|
Виробництво сталі
Лекція 15
Тема: «Виробництво чавуну і сталі»
План лекції
1 Виробництво чавуна
2 Виробництво сталі
1 Виробництво чавуна Чавун виплавляють у вертикальних печах шахтного типу - доменних почах. Сутність процесу отримання чавуну в доменних печах полягає у відновленні оксидів заліза, що входять до складу руди, яку завантажують у піч, окисом вуглецю, воднем і твердим вуглецем, що виділяються при згоранні палива в печі. Пристрій і робота доменної печі. Корисна висота доменної печі досягає до 80 м / Солнцев, с. 16 /, або приблизно в 2,5 ... 3 рази більше діаметра. Робочий простір печі включає колошник 6, шахту 5, распар 4, заплечики 3, горн 1, поду 15. У верхній частині колошника знаходиться засипний апарат 8, через який в піч завантажують шихту (офлюсований агломерат і окатиші). Стінки печі викладають з вогнетривких матеріалів - в ос новних з шамоту. Нижню частину горна і його підставу (поду) виконують з особливо вогнетривких матеріалів - вуглецевих (графітизованих) блоків. Для підвищення стійкості вогнетривкої кладки в ній встановлюють (приблизно на 3Д висоти печі) металеві холодильники, по яких циркулює вода. Для зменшення витрат води (для великих печей витрата води до 70000 м3 на добу) застосовують випарне охолодження, засноване на тому, що поглинання-ться тепло використовується для пароутворення. Кладка печі зовні укладена в сталевий кожух товщиною до 40 мм. Для зменшення навантаження на нижню частину печі її верхню частину (шахту) споруджують на сталевому кільці, спирається на ко лонни. Доменна піч (рис. 1.4) має сталевий кожух, викладений зсередини вогнетривкою шамотною цеглою. Схема роботи доменного цеху сучасного металургійного за вода приведена на рис. 1.5. Шихтові матеріали надходять в бункера, розташовані на рудному дворі: офлюсований агломерат-с агломераційної фабрики, а кокс - від коксових батарей коксохімічного заводу. З бункерів шихтові матеріали подаються в вагон-ваги 1, на яких зважують певні порції шихти. З вагона-ваг кокс і агломерат передаються в вагонетку 3 скіпового підйомника. Скиповий под приймач являє собою похилий рейковий міст, по якому дви жутся дві вагонетки. Скіп піднімається сталевим канатом до верхньої точки рейкового моста і перекидається. Через завантажувальний пристрій во (засипний апарат) 4 шихта потрапляє в доменну піч (див. рис. 1.5). Піч складається з колошника 5, шахти б, распара 7, заплічок 8 і горна 9. Дві скіпові вагонетки за допомогою лебідки пересуваються по похилому мосту 12 (див. рис. 1.4) до засипний апарат 8 і, перекидаючись, висипають шихту в приймальню воронку 7 розподільника шихти. При опусканні малого конуса 10 засипного апарату шихта потрапляє в чашу 11 а при опусканні великого конуса 13 - в доменну піч. Така послідовність роботи механізмів засипного апарату необхідна для запобігання виходу газів з доменної печі в атмосферу.
| | |
Рис. 1.4. Схема пристрою доменної печі і воздухонагревателя
Для рівномірного розподілу шихти в доменній печі малий конус і приймальня воронка після завантаження чергової порції матеріалів повертаються на кут, кратний 60 °. Всі механізми засипного апарату і скіпового підйомника Агломерат, руду, флюс і кокс, які надходять в піч у певному співвідношенні, називають шихтою. Доменні печі, як і всі шахтні печі, працюють за принципом протитечії. Зверху сходять шихтові матеріали, а знизу їм назустріч рухаються гази, що утворюються в процесі горіння палива.
Рис. 1.5. Схема роботи доменного цеху
В процесі роботи печі шихтові матеріали поступово опускаються вниз, а через завантажувальний пристрій у піч подаються нові порції шихтових матеріалів у такій кількості, щоб весь корисний об'єм печі був заповнений. Корисний об'єм печі - це об'єм, який займає шихтою від поду до нижньої кромки великого конуса засипного апарату при його опусканні. Сучасні доменні печі мають корисний об'єм 2000 ... 5000 м3 Корисна висота доменної печі досягає 35 м. У верхній частині горна знаходяться фурмені пристрою 14 через які в піч надходять нагріте повітря, необхідний для горіння коксу, і газоподібне паливо, в деяких випадках рідке або пиловидне паливо . Попередній нагрів повітря необхідний для зменшення втрат теплоти в печі. Повітря поступає в доменну піч з повітронагрівачів. Для нагрівання повітря застосовують повітронагрівачі регенеративного типу. Усередині воздухонагревателя (рис. 1.4, праворуч) є камера згоряння 2 і насадка 4 займає основний обсяг воздухонагревателя. Насадка викладена з вогнетривких цеглин 3 так, що між ними утворюються вертикальні канали. У нижню частину камери згоряння до пальника 1 подається очищений від пилу Колошниковим газ, який згорає і утворює гарячі гази. Гарячі гази, проходячи через насадку, нагрівають її і видаляються з воздухонагревателя через димову трубу. Потім подача газу до пальника припиняється, і по трубопроводу через насадку пропускається холодне повітря, що подається турбовоз-духодувной машиною. Доменна піч має кілька повітро нагрівачів: у той час як в одних насадка нагрівається горя чими газами, в інших вона віддає теплоту холодному повітрю, нагріваючи його. За охолодженні нагрітої насадки повітрям нагрівачі перемикаються. Повітря, проходячи через насадку повітро - нагрівача, нагрівається до 1000 ... 1200 ° С і надходить до фурменої пристрою 14 доменної печі (див. рис. II.2), а звідти в її робочий простір. Горіння палива. Поблизу фурм 2 (див. рис. 1.4) вуглець коксу, взаємодіючи з киснем повітря, згоряє: С + О2 = СО2 + 393,51 кДж. При високих температурах і в присутності твердого вуглецю коксу двоокис вуглецю нестійка і частково переходить і окис вуглецю; СО2 + С = 2СО - 171,88 кДж. Одночасно, на деякій відстані від фурм, йде реакція неповного горіння вуглецю коксу: С - 1/2О2 = СО + 110,5 до Дж. В результаті горіння коксу в доменній печі виділяється теплота і утворюється газовий потік, що містить СО, СО2 та інші гази. При цьому в печі трохи вище рівня фурм температура стає більш 2000 ° С. Гарячі гази, піднімаючись вгору, віддають свою теплоту шихтовим матеріалами і нагрівають їх, охолоджуючись до 400 ... 300 ° С у колошника. У зоні печі, де температура газон досягає 700 ... 450 ° С, частина окису вуглецю розкладається з утворенням сажисті вуглецю, що осідає на шихтових матеріалах: 2СО = СО2 + С ↓ Інша частина газу, що складається в основному з СО, СО2, N2, Н2, СН4 (колошниковим газ), відводиться з печі по трубах і після очищення використовується як паливо для повітронагрівачів. Шихтові матеріали (агломерат, кокс) опускаються назустріч потоку газів і нагріваються. В результаті в них відбувається цілий ряд хімічних перетворень: віддаляється волога, з палива виділяються летючі речовини, а при прогріванні шихти до температури ~ 570 ° С починається основний процес - відновлення оксидів заліза, що містяться в агломерате.
Відновлення оксидів заліза в доменній печі. Цей процес протікає в результаті взаємодії оксидів заліза з окисом вуглецю і твердим вуглецем коксу, а також воднем. Відновлення твердим вуглецем називають прямим, а газами - непрямим. При температурах до 570 ° С відновлення окису заліза протікає по реакціях ЗFe2О3 + СО = 2Ге3О4 + СО2; Fе3О4 + 4СО = ЗFе + 4СО2. При більш високих температурах (750 ... 900 ° С) оксиди заліза відновлюються найбільш інтенсивно: ЗFе2Оз + СО = 2Fе3О4 + СО2; Fе3О4 + СО = ЗFеО + СО2; FeО + СО = Fе + СО2. При цих температурах з руди, що знаходиться в нижній зоні шахти доменної печі, утворюється тверде губчасте залізо. Деяка частина закису заліза опускається до рівня распара і заплічок, де відновлюється твердим вуглецем коксу в результаті двох одночасно протікаючих реакцій: СО2 + С = 2СО; FеО + СО = Fе + СО3 FеО + C = Fe + CO В реакціях відновлення заліза беруть участь також сажистий вуглець і водень, особливо при введенні в доменну піч природного газу. У міру опускання шихта досягає зони в печі, де температура становить 1000 ... 1100 ° С. При цих температурах відновлене з руди тверде залізо, взаємодіючи з окисом вуглецю, коксом і сажистий вуглецем, інтенсивно науглероживается завдяки здатності заліза у твердому стані розчиняти вуглець: ЗFе + 2СО = Ге3С + СО2; ЗFe + С = Fе3С. При насиченні вуглецем температура плавлення заліза знижується і на рівні распара і заплічок воно розплавляється. Краплі залізовуглецевих сплаву, протікаючи по шматках коксу, додатково насичуються вуглецем (до 4% і більше), марганцем, кремнієм, фосфором, які відновлюються з руди, а також сірої, що міститься в коксі. Ці процеси протікають слідую щим чином. Марганець міститься в руді у вигляді МnО2, Мn2О3, Мп3О4. Ці сполуки легко відновлюються до МnО. При температурі більше 1000 ° С частина МnО відновлюється твердим вуглецем по реакціях МnО + СО = Мn + СО2; СО2 + С = 2СО
МnО + С = Мn + СО Одночасно марганець взаємодіє з твердим вуглецем і утворює карбід Мn3С, підвищуючи вміст вуглецю в сплаві. Інша частина МnО входить до складу шлаку. Кремній, що міститься в порожній породі руди у вигляді SiO2, температурі вище 1100 0С також частково відновлюється твердим вуглецем: SiO2 + С = SiO + СО; SiO + С = Si + СО SiO2 + 2С = Si + 2СО Утворився кремній розчиняється в залозі. Інша частина SiO2 також входить до складу шлаку. Фосфор міститься в рудо у вигляді сполук (FеО) 3Р2О5 і (СаО) 3Р2О5. Частково фосфат заліза відновлюється окисом вуглецю: 2Fе3 (РО4) 2 + 16СО = 2Fе3Р + 2Р + 16СО2. При температурах понад 1000 ° С відновлення йде за рахунок твердого вуглецю: 2Fе3 (РО4) 2 + 16С = ЗFе3Р + 2Р + 16СО. При температурах вище 1300 ° С фосфор відновлюється з фосфату кальцію: (СаО) 3Р2О5 + 5С = ЗСАТ + 2Р + 5СО. Утворився фосфід заліза (Fе3Р) і фосфор повністю розчиняються в залозі і входять до складу чавуну. Сірка присутня в коксі і руді у вигляді органічної сірки та сполук FeS2, FеS, СаSО4. Сірка летуча і тому частина її віддаляється з газом при нагріванні шихти в печі. Сірка з коксу окислюється у фурм киснем дуття до SО2 і, піднімаючись з газами, відновлюється твердим вуглецем: SО2 +2 С = S + 2СО. При цьому частина сірки у вигляді 8 і Ге8 розчиняється в чавуні. Сірка є шкідливою домішкою і погіршує якість чавуну. Для видалення сірки прагнуть підвищити вміст СаО в шлаку. При цьому частина сірки у вигляді Са8 віддаляється в шлак по реакціях FеS + СаО = Са + FеО, FеО + С = Fе + СО. Таким чином, в результаті процесів відновлення оксидів заліза, частини оксидів марганцю і кремнію, фосфатів і сер ність сполук, розчинення в залозі С, Мn, Si, Р, S в печі утворюється чавун. У нижній частині печі утворюється шлак в ре док сплаву окислів порожньої породи руди, флюсів і золи палива. В умовах доменного процесу оксиди Аl2О3, СаО, МgО, що містяться в порожній породі руди, повністю переходять в шлак. У шлаку міститься також частина невосстановівшіхся оксидів SiO2, МnО, FеО і Са. Шлак утворюється поступово, його склад змінюється в міру набрякання в гори; де він накопичується на поверхні рідкого чавуну завдяки меншій щільності. Склад шлаку залежить від складу застосовуються шихтових матеріалів і виплавленого чавуну.
У міру скупчення чавуну і шлаку їх випускають з печі. Чавун випускають через 3 ... 4 год, а шлак через 1,0 ... 1,5 ч. Чавун випускають через чавунну летку 16 (див. рис. 1.4, отвір в кладці, розташоване вище поду), а шлак - через жужільну летку 17. Чавунну летку відкривають бурильної машиною, а після випуску чавуну закривають вогнетривкої масою. Чавун і шлак зливають по жолобах, прокладених по ливарному двору, в чугуновозні ковші і шлаковозів чаші, встановлені на залізничних платформах. Ємність чавуновозних ковшів 90 ... 140 т. У них чавун транспортують в киснево-конвертерний або мартенівські цехи для переділу в сталь. Чавун, не використовується в рідкому вигляді, надходить на розливні машини. З ковша чавун через передавальний жолоб заповнює металеві форми-виливниці розливної машини і твердне в них у вигляді чушок-злитків масою 45 кг. Часто рідкий шлак з доменної печі не зливають в шлаковозів чаші, а для зручності подальшого використання піддають мокрій грануляції: на нього направляють струмінь води, сприяння з дією якої він розсипається на дрібні гранули. Продукти доменної плавки. У доменних печах отримують два рідких продукту - чавун і шлак, а також колошниковим газ. Чавун - основний продукт доменної плавки. У доменних печах отримують чавун різного хімічного складу в залежності від його призначення. Передільний чавун виплавляють для переділу його в сталь в конвертерах чи мартенівських печах. Він містить 4,0 ... 4,4% С; до 0,6 ... 0,8% Si; до 0,25 ... 1,0% Мn; 0,15 ... 0,3% Р і 0,03 ... 0, 07% S. Передільний чавун деяких марок, предназ начення для переділу в сталь в конвертерах, має знижений вміст фосфору (до 0,07%). Ливарний чавун використовують для переплавки його на ма машинобудівний заводах при виробництві фасонних виливків. Він містить підвищену кількість кремнію (до 2,75 ... 3,25%). Крім чавуну, в доменній печі виплавляють феросплави. Доменні феросплави - сплави заліза з крем ням, марганцем та іншими металами. Їх застосовують для рас кісленія і легування стали. До них відносяться: доменний феросиліцій з 9 ... 13% Si і до 3% Мn; доменний феромарганець з 70 ... 75% Мn і до 2% Si; дзеркальний чавун з 10 ... 25% Мn і до 2% Si. Побічними продуктами доменної плавки є шлак і колошниковим газ, також використовуються у виробництві. З шлаку виробляють шлаковату, шлакоблоки, цемент, а колошниковим газ після очищення від пилу використовують як паливо для нагрівання повітря, вдуваемого в доменну піч, а також у цехах металургійних заводів. Найважливіші техніко-економічні показники. Такими показниками роботи доменних печей є коефіцієнт вико користування корисного обсягу доменної печі (К. І. II. О) і питома витрата коксу. Коефіцієнт використання корисного об'єму печі (К. І. П. О. в м3 / т) визначається як відношення корисного об'єму печі V (в м3) до її середньодобової продуктивності Р і тоннах виплавленого чавуну. К. І. П. O. = V / P Чим вища продуктивність доменної печі, тим нижче К. І. П. О., який для більшості доменних печей в нашій країні становить 0,5 ... 0,7. Питома витрата коксу K - відношення витрат А коксу за добу до кількості Р в тоннах передільного чавуну, виплавленого за той же час: У нашій країні питома витрата коксу в доменних печах становить 0,5 ... 0,7; він є важливим показником роботи доменної печі, так як вартість коксу складає більше 50% загальної вартості чавуну
Виробництво сталі
Сталь - ції стоп заліза з вуглецем, у якому масова Частка вуглецю не пере віщує 2,14%. Крім заліза й вуглецю у сталі Завжди є марганець (до 0,8%), кремній (до 0,4%), фосфор (до 0,07%) та сірка (до 0,06%), Що пов'язано з особливостях технології її виробництва.
Суть процесу Основною сировина для масового виробництва сталі є переробній чавун и скрап (металобрухт, металеві відходи металургійніх та машінобудівніх за водів). Чавун порівняно Зі Сталл містіть Більшу кількість вуглецю, марганцю, кремнію, фосфору й Сірки. Позбутісь надлишки вуглецю, марганцю, кремнію и фосфору можна шляхом їх оксідації. Під час оксідації вуглець під видом газоподібного оксиду вуглецю СО виходили в атмосферу, а марганець и кремній утворюють нерозчінні в розтопленому металі оксиди Фосфор оксідується, та сполучаючісь з флюсом СаО, переходити у нерозчінній у металі фосфат кальцію. Сірку з розчинення в металі сульфіду заліза переводять у нерозчінній сульфід кальцію. Утворені сполуки (МПО, 5іО "(СаО) 3-Р, О5), які ма ють менше від заліза густин, випливають на поверхню Як шлак.
Тенденції розвитку виробництва сталі у 20 ст. Попро все Ширшов Використання в народному господарстві стопів кольо-рових металів, пластмас и композитних матеріалів, сталь залішається Основним конструкційнім матеріалом Завдяк Кращим механічнім и технологічнім властівостям та порівняно невісокій вартості. Жодних з промислове розвинутих країн світу не обходиться без власного виробництва сталі. Обсягах виробництва стілі та йо технології є Важливим характеристикою промислового потенціалу кожної держави. Існує три Основні способу виробництва сталі - - киснево-конверторний - мартенівській - виробництво сталі в електропечах Очевидно, Що Попит на сталь, вітоплену тім чи іншім способом, візначається її ціною и властівостямі.
Киснево-конверторний метод Киснево конвертор складається Із Сталевого кожуха 2 (рис. 1.2.3), звареного ч листа, ОСНОВНОЇ футеровки 3 та відчини 5 для вілівання сталі. Конвертор має іііііфі (на малюнку не показані) з горизонтальною віссю, навколо якої можна Ного повертаті для завантаження скрап, наливання чавуна, насіпання флюсу І 'шлі'ліої руди й вілівання сталі та шлаку. Конвертор вміщує від 100 до 400 т рідкого чавуна. Шихтовими матеріалами для киснево-конверторного процесу службовців: рідкій переробній чавун (понад 70%), скрап (до 25%), Залізна руда (до 10%), вапняка СаО, а кож плавиковий шпат СаF2, - для розрідження шлаку. Перед вітоплюванням конвертор нахіляють для завантаження скрапу. Далі налівають чавун, Що має температуру 1300 ... 1450 ° С. Потім конвертор повертаються у вертикальне положення, в нього вставляють водоохолоджувану фурму 4, через Яку вдувають Кисень (99,5 ... 99,8%) підтіском 0,9 .. .1,4 МПа. Водночас у конвертор насіпають залізну руду, вапняка и плавиковий шпат. Струмінь кисня пронікає вглиб металу й віклікає оксідацію. Час продування кісним становіть 12 ... 25 хв, а трівалість одного вітоплювання - ЗО ... 55 хв
| Після наливання чавуна почінається розтоплювання скрап, температура в конверторі поступово підвіщується за рахунок тепла реакцій оксідації, Що віклікані вдування кисня. Оскількі на качани температура ванни відносно низько, то за принципом Ле Шательє активно відбуваються екзотермічні реакції. Внаслідок того, Що концентрація заліза у ванні Дуже висока, то за законом діючіх мас, йо оксідація Йде Дуже інтенсівно: Fе + О, = 2FеО Утворення оксид заліза FеО розчіняється у металі й реагує з більш спорід-ненімі з кісним, Ніж залізо, елементами - кремнієм, фосфором и марганцем: 2 Fе О + Sі = 2Fе + SiO 2, 2 FеО + 2Р = 5Fе + Р2О5 Fе О + Мn = Fе + МnО Оксиди SiO 2 и МПО погано розчіняються в металі І, маючи менше густин, випливають на йо поверхні, утворюючі шлак. Фосфорний ангідрід Р2О5, вступивши в реакцію з оксидом кальцію СаО, утворює фосфід кальцію, Який кож переходити у шлак:
Р2О5 + ЗСАТ = (СаО) 3 * Р2О5
Вміст фосфору в шлаці Швидко зростає, набліжаючісь до насічення. Щоб продовжіті дефосфорізацію, вілівають шлак и насіпають свіжу порцію СаО. Завдяк реакціям (1.2.1 ... 1.2.5) температура металу помітно підвіщується, акти-візуючі оксідацію вуглецю: FеО + С = Fе + СО (1.2.6) Бульбашки СО, піднімаючісь вгору, добро перемішують ванну, вірівню ють склад и температуру металу та спріяють вилучення газів й неметалевіх включення. Наявний у металі вуглець и оксид заліза спріяють перебігу реакції (1.2.6), внаслідок Чого у майбутнє злітку залішається безліч порожнина, Заповіт неніх СО. Сталь з такими порожнина назівають кіплячою. Ці порожнина можут спричиняти кріхке руйнування при низьких температурах. Щоб змен шити небезпеку такого руйнування, необхідно усунуті причину кіпіння сталі шляхом дезоксідації, тоб Відновлення FеО до чистого заліза за допомога марганцю, кремнію и алюмінію. Зовсім дезоксідовані сталі назівають спокійні ми, а Частково дезоксідовані - напівспокійнімі. Дезоксідацію здійснюють у ковші под годину випуску сталі з конвертора в такій послідовності: Спочатку феромарганцем, потім - феросіліцієм и напрікінці алюмінієм:
Переваги киснево-конверторного виробництва сталі - Порівняно нізькі капіталовкладення на спорудження киснево-конверторних цехів; - Висока продуктівність; - Отримай сталь не поступається за якістю мартенівській - Можна переробляті значную кількість (до 25%) скрап; -Непотрібнопаліва.
- Недолікі: - - Значні Втрати металу на вігар; - Труднощі, пов'язані з вітоплюванням сталей, Що містять легкооксідівні Елементи; - Процес вімагає значної кількості (до 80%) рідкого чавуна. Техніко-економічні показники виробництва сталі в киснево конверторах До головних техніко-економічних показніків виробництва сталі в киснево конверторах належать: продуктівність конвертора, витрати кисня на одиницю продукції, вихід рідкої сталі ТОЩО. Продуктівність велікотонажніх конверторів на 250 ... 400 т сягає 400 ... 500 т сталі за годину, Що істотно перевіщує Цю ж характеристику мартенівськіх чи електросталевитоплювальних печей. Витрати кисня колівається в межах 47 ... 57 м3 на тонну вітопленої сталі. Вихід рідкої сталі відносно Масі металу в шіхті становіть 89 ... 92%. Плавка в мартенівських печах. У мартенівських печах сталь виплавляють з твердого або рідкого чавуну, сталевого і чавунного брухту, окислених і металлізованних окатишів з добавками же-корисної руди, окалини, флюсів та феросплавів; при цьому отримують побічний продукт - мартенівський шлак. Мартенівська піч представлена на рис. 6. Її плавильне про странство 4 обмежена знизу подини 7, зверху - склепінням 3, с бо ков - стінками. По обидві сторони плавильного простору на ходяться головки / і 5 з каналами, що ведуть до шлаковиках (на рис.6 не показані) для затримання пилу та бризок шлаку, захоплений них з плавильного простору відходять газами. Шлаковики повідомляються з регенераторами 6 і 9, які мають вогнетривку насадку для підігріву окисного дуття і газового палива.
| На метал гійної заводах печі нагрівають спалюванням природного газу або суміші доменного та коксового газів. Вступники по каналах 2 гази змішуються до згорають в робочому просторі довгим Факе лом. Періодично (через 10-15 хв) напрямок руху газів в регенераторах, головках і самому робочому просторі изме вується на зворотне; така схема забезпечує постійний підігрів вступників газів і температуру в плавильному просторі до 1700 ° С. У передній стінці мартенівської печі знаходяться вікна 8, через які з робочої площадки завалюють шихту, беруть проби сталі і спостерігають за плавкою. Подина печі нахилена до задньої стінки, в якій знаходиться річка, закрита під час плавки пробкою з вогнетривкої маси; для випуску стали пробку зовні пробивають, Мартенівські печі на машинобудівних заводах працюють на природному газі або мазуті, який для подачі в плавильний простір розпорошується форсунками. Мартенівський процес зводиться до фізико-хімічним взаємо дії між металом, шлаком, газовим середовищем і частково вогні упорами печі. Завданням процесу є доведення в стали вугіллі роду, марганцю, кремнію до встановленої кількості і можливо більш повне видалення шкідливих домішок при найменших изна вування печі і витратах палива. Окислення металу протікає при взаємодії його з кисло родом, що надходять в піч у складі окисного дуття, а також з рудою і окалиною. Для прискорення окислення застосовують також вдування кисню в розплавлений метал. Основними різновидами мартенівської плавки є скрап-рудний процес і скрап-процес. Скрап-рудний процес ведеться на металургійних заводах (комбінатах), де працюють також доменні печі. Металева шихта складається з 60-80% рідкого чавуну і 20-40% скрапу. Для мартенівського чавуну характерно підвищений масове содер жание фосфору, тому скрап-рудний процес є основним. Скрап-процесом виплавляють сталь у мартенівських печах ма машинобудівний заводів, де накопичуються відходи виробниц ства: стружка, обрізки, брак, лом. При скрап-процессе металеві ська шихта складається з 65-80% скрапу і чушкового переробного чавуну. Основний скрап-процес по реакціях, що протікають після розплавлення шихти, подібний скрап-рудному процесу. У мартенівських печах виплавляють вуглецеву конструкційн ву і леговану сталі різних марок. Мартенівські печі працюють циклами, але нагрів печі ведеться безперервно, тому підготовка нової плавки стали починається з огляду печі та усунення ня вад у подині і бічних укосах печі шляхом їх заварки новим шаром доломіту або магнезиту ще під час випуску попередньої плавки. Рідкий чавун завантажують в піч через вікно за допомогою вставляється сталевого жолоби, футерованого зсередини вогнетривом. Чавун заливають у піч, коли тверда шихта прогріта і починає оплавлятися. З заливанням рідкого чавуну різко прискорюється плавлення твердої металеві ської частини шихти. Одночасно з прогріванням шихти на чинается окислення домішок. До моменту розплавлення шихти майже повністю окислюється кремній, більш по Ловін марганцю, третя частина фосфору і частково вугіллі род. Окислення вуглецю в ще не прогрітій ванні викликає спінювання шлаку. Цим користуються для видалення з печі самопливом через пороги завантажувальних вікон частини пер-первинного шлаку. Після розплавлення шихти на чинается доведення сталі. У печі утворюється ванна металу, покрита зверху шаром шлаку, що містить значну кількість оксидів заліза, які завдяки перемі вування ванни потрапляють в метал і окислюють домішки, в тому числі і вуглець. Утворений СО у вигляді газових бульбашок добре перемішує ванну і сприяє виділенню з ме талу газових та інших включень. Процес виділення «чадного газу» називають «кипінням» ванни. В цей же період з шихтових матеріалів видаляють фосфор шляхом періодичного скачування шлаку. Для успішного видалення фосфору необхідно мати в шлаку максимальну кількість вапна. Процес доводки металу до потрібного хімічного со става проводиться в так званий період чистого ки співу металу, що починається після припинення доба-вок в нього залізної руди. Чисте кипіння ванни протікання кає не менше 1 ч. Готовність заданої плавки стали визна чають взяттям проби та експрес-аналізом. Після цього проводиться розкислення і випуск сталі в ковші, з яких її розливають у злитки. Загальна про тривалість отримання сталі в мартенівської печі займає кілька годин. Розкислювання стали у ванні березня теновской печі проводять спочатку доменним ферромарган цем, а потім феросиліцію. сталь починають випускати з печі і завершують розкислення в ковші, закидаючи в нього шматки багатого феросиліцію (45 або 75% 51) і алюмінію або сілікоалюмінія. Алюміній є активним розкислювачем стали, але утворюється А] 2О3 тугоплавок і у вигляді тонкої суспензії майже весь залишається в сталі. Прийнято вважати, що ці частинки А12О3 служать центрами кристалізації при формуванні зливка, і зі збільшенням кількості алю Мінія, що вводиться для розкислення, можна отримати більш дрібну структуру злитка або відливання. Головна перевага мартенівського способу - його універсальність як в можливості виплавки широкого сортаменту вуглецевих і легованих сталей, так і у використанні вихідних матеріалів. Основними недоліками мартенівського процесу сле дме вважати більшу тривалість процесу і значна витрата палива. Тому важлива автомати-зація мартенівських печей, особливо їх теплового режиму.
Виробництво сталі в електропечах Електроплавильні печі. Ці печі мають переваги порівняно з іншими плавильними агрегатами. В електропечах можна отримати високу температуру, створювати окисну, відновлювальну, нейтральну атмосферу або вакуум. У цих печах можна виплав лять сталь і сплави будь-якого складу, більш повно розкислити метал з утворенням мінімальної кількості неметалічних включень-продуктів розкислення. Тому електропечі викорис товують для виплавки конструкційних сталей відповідального наз чення, високолегованих, інструментальних, корозійно-стійких (нержавіючих) та інших спеціальних сталей і сплавів. Для плавки сталі використовуються дуговими і індукційні електропечі. Дугова електросталеплавильна піч. У цих печах в якості джерела теплоти використовують електрич ний дугу, що виникає між електродами і металевою шихтою. Дугова електросталеплавильна піч (рис. 1. 10) пита ється трифазним змінним струмом і має три циліндричних електрода 9, виготовлених з графітованої маси. Електрич ний струм від трансформатора гнучкими кабелями 7 і мідними шинами підводиться до електродотримача 8, а через них до елек Трод 9. Між електродами і металевою шихтою 4 метушні кає електрична дуга, електроенергія перетворюється в теплоту, яка передається металу і шлаку випромінюванням. Робоче напря ються 180 ... 600 В, сила струму 1 ... 10 кА. Під час роботи печі довжина дуги регулюється автоматично шляхом вертикаль ного переміщення електродів. Піч має сталевий зварної кожух 3. Кожух печі зсередини футерований теплоізоляційним і вогнетривкою цеглою 7, який може бути основним (магне зітовий, магнезітохромітового) або кислим (динасовий). За дина 12 печі набивається вогнетривкої масою. Плавильне про простір обмежена стінками 5, подини 12 і склепінням 6, виготов ється також з вогнетривкої цегли та мають отвори для проходу електродів. У стінках печі є робоче вікно 10 для управління ходом плавки і льотка для випуску готової стали по жолобу 2 в ківш.

Рис. 1.10. Схема дугового електричної плавильної печі
Піч завантажують при знятому склепінні. Механізмом 11 піч може нахилятися в бік завантажувального вікна і річки. Ємність дугових електропечей 0,5-400 т. У металургійних цехах зазвичай використовують дугові електропечі з основною футеровкою, а в ли тейнах цехах - з кислою. Основна дугова піч. Застосовують два види технології плавки в дугового основний печі: на шихті з легуючих ванних відходів (методом переплавки) і на вуглецевої шихті (з окисленням домішок). Плавку на шихті з легованих відходів з низьким утримуючи ням фосфору проводять без окислення домішок. Шихта для такої плавки, крім зниженого змісту фосфору, повинна мати менше, ніж у сталі, що виплавляється, кількість марганцю і крем ня. По суті це переплав. Проте в процесі плавки за рахунок кисню деякі домішки (алюмінію, титану, кремнію, мар ганця, хрому) окислюються. Крім того, шихта може містити оксиди. Тому після розплавлення шихти метал раскисляют, видаляють сірку, наводять основний шлак, при необхідності на углерожівают і доводять метал до заданого хімічного складу. Розкислють феросиліцію, алюмінієм, меленим коксом. При цьому оксиди легуючих елементів відновлюються і пере ходять з шлаку в метал. Таким способом плавки одержують леги рова стали з відходів машинобудівних заводів. Плавку на вуглецевої шихті частіше застосовують для вироб ництва конструкційних вуглецевих сталей. Цю плавку про водять за два періоди: окислювальний і відновний. Після заправки печі, видалення залишків металу і шлаку попередньої плавки, виправлення пошкоджених місць футеровки в піч загру-жають шихту: сталевий брухт (до 90%), чушковий передільний чу гун (до 10%), електродний бій або кокс для науглероживания металу і 2 ... 3% вапна. Після закінчення завалки шихти електроди опускають вниз і включають струм; шихта під електродами плавиться, метал накопичується на подині печі. Під час плавлення шихти починається окислювальний період плавки: за рахунок кисло роду повітря, окислів шихти і окалини окислюється кремній, марганець, вуглець, залізо. Разом з окисом кальцію, содер жащейся в вапна, оксиди цих елементів утворюють основний залозистий шлак, що сприяє видаленню фосфору з металу. Після нагрівання металу і шлаку до 1500 ... 1540 ° С в піч загру жають руду і вапно. Що міститься в руді кисень інтенсивно окисляє вуглець і викликає кипіння ванни рідкого металу за рахунок виділяються пухирців окису вуглецю. Шлак спінить ється, рівень його підвищується; для випуску шлаку піч нахилу няют в бік робочого вікна і він стікає в жужільну чашу. Кипіння металу прискорює нагрівання ванни, видалення з металу газів, неметалевих включень, сприяє видаленню фос-фора. Шлаки видаляють, руду і вапно додають 2 ... 3 рази. В ре док вміст фосфору в металі знижується до 0,01% і од новременно за рахунок утворення окису вуглецю при кипінні зменшується і вміст вуглецю. Коли зміст вуглецю стає менше заданого на 0,1%, кипіння припиняють і повністю видаляють з печі шлак. Цим закінчується окисли ний період плавки. Відновлювальний період плавки включає розкислення ме талу, видалення сірки і доведення хімічного складу до заданий ного. Після видалення окислювального шлаку в піч подають фер ромарганец в кількості, що забезпечує заданий вміст марганцю у сталі, а також виробляють коксування, якщо виплавляють високовуглецеві стали (до 1,5% С). Потім в піч завантажують флюс, що складається з вапна, плавикового шпату і шамотного бою. Після розплавлення флюсів та освіти шлаку в піч вводять розкислюючу суміш, що складається з ви вести, плавикового шпату, меленого коксу і феросиліцію. Мелена кокс і феросиліцій вводять в порошкоподібному вигляді. Вони дуже повільно проникають через шар шлаку. У шлаку відновлюється закис заліза: FeO + C = Fe + CO; 2FeO + Si = Fe + SiO2 При цьому зміст закису заліза в шлаку знижується і вона з металу відповідно до закону розподілу починає переходити в шлак. Цей процес називають дифузійним раскислением стали. Розкислюючу суміш вводять в піч кілька разів. У міру розкислення і зниження вмісту FеО колір шлаку з змінюється і він стає майже білим. Розкислювання під білим шлаком триває 30 ... 60 хв. Під час відновного періоду сірка видаляється з ме талу, що пояснюється високим (до 55 ... 60%) вмістом СаО в білому шлаку і низьким (менше 0,5%) вмістом FеО. Це спо собствует інтенсивному видаленню сірки з металу: FeS + CaO = CaS + FeO. По ходу відновного періоду беруть проби для визна ділення хімічного складу металу. При необхідності в піч вводять феросплави для досягнення заданого хімічного со става металу. Коли досягнуті задані склад металу і тим пература, виконують кінцеве розкислення стали алюмінієм і силікокальцієм. Після цього слід випуск металу з печі в ківш. При виплавці легованих сталей в дугових печах в сталь вводять легуючі елементи у вигляді феросплавів. Порядок введення визначається спорідненістю легуючих елементів до кисню. Нікель, молібден мають менший спорідненістю до кисню, ніж залізо, і їх вводять в період плавлення або в окислювальний період. Хром легко окислюється і його вводять у відновний період; кремній, ванадій, титан - перед випуском металу з печі в ківш, так як вони легко окислюються. Техніко-економічні показники. Ці показники плавки в дугових печах залежать від ємності печі і технології плавки. Витрата електроенергії на 1 т сталі залежить від ємності печі. Зі збільшенням ємності печі витрату електроенергії на 1 т виплав ленній стали зменшується. Наприклад, для печі ємністю 25 т він становить 750 кВт-год, а для печі ємністю 100 т -575 кВт-ч. Витрата графітованих електродів становить 6-9 кг / т виплав ленній стали. Техніко-економічні показники роботи дугових печей і якість металу підвищуються за рахунок інтенсифікації плавки, збільшення ємності печі, потужності трансформаторів, механізації завантаження шихти, застосування електромагнітного перемішування металу. Значною ефективності можна досягти при виплавці легованих сталей, застосовуючи дуплекс-процес: виплавка сталі в основному кисневому конвертері, а рафінірова ня і доведення по хімічному складу в електропечі. Ефективним є застосування кисню для продувки ванни стали в окислювальний період, що інтенсифікує процес плавки, збільшує на 15 ... 20% виробник ність печі, знижує витрату електроенергії і економить легуючі добавки.
Електроіндукціонние печі. Індукційна тигельна стале плавильна піч (рис. 1.11) складається з водоохолоджуваних індук тора 5, усередині якого знаходиться тигель 4 з металевою шихтою. Через індуктор проходить однофазний змінний струм підвищеної частоти (500 ... 1000 кГц). Ток створює змінний магнітний потік, пронизуючи шматки металу в тиглі, наводить в них потужні вихрові струми (Фуко), що нагрівають метал 1 до розплавлення і необхідних температур перегріву. Тигель може бути виготовлений з кислих (кварцит) або основних (магнезитовий порошок) вогнетривких матеріалів. Ємність тигля від 60 до 25 т. Ток до індуктора підводиться від генератора високої частоти-лампового (лабораторні печі) або машинного. Для зменшення втрат теплоти при плавленні можна застосувати знімний звід 2. Індукційні печі мають переваги перед дуговими: 1) у них відсутня електрична дуга, що дозволяє виплавляти метали з низьким вмістом вуглецю, газів і малим чадом елементів, це особливо важливо при виплавці високоякісних них сталей і сплавів;
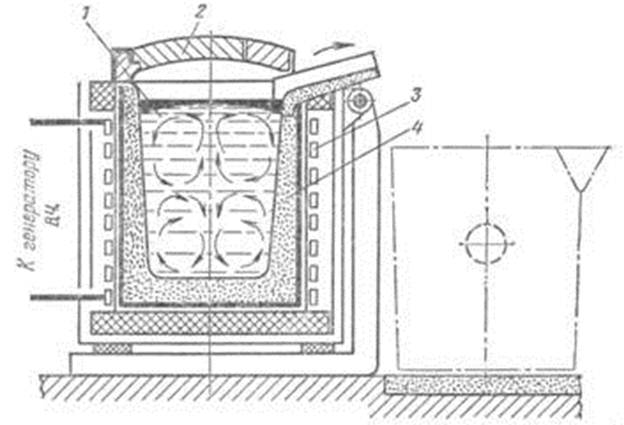
Рис. 1.11. Схема індукційної тигельної електричної плавильної печі 2) при плавці в металі виникають електро динамічні сили, які перемішують метал в печі і спо собствует вирівнювання хімічного складу, Спливання Неме вих включень; 3) індукційні печі мають невеликі габаритні розміри, що дозволяє розміщати їх в закриті ка заходи, в яких можна створювати будь-яку атмосферу, а також вакуум. Однак ці печі мають малу стійкість футеровки, шлак в них нагрівається теплотою металу і температура його не достатня для інтенсивного протікання металургійних про процесів між металом і шлаком. Зазвичай в індукційних печах виплавляють сталь і сплави або з легованих відходів методом переплавки, або з чистого шихтового заліза і скрапу з добавкою феросплавів методом сплавлення. У більшості випадків печі мають кислу футеровку. Основну футеровку використовують для виплавки сталей і спла вов з високим вмістом марганцю, нікелю, титану та алюмінію ня. При завантаженні ретельно підбирають хімічний склад шихти відповідно до заданого, так як плавка протікає швидко, і пов ного аналізу металу по ходу плавки не роблять. Тому необ ходимое кількість феросплавів (Ферровольфрам, ферромо-Либідь, феррохром, нікель) для отримання заданого хімічного складу металу завантажують на дно тигля разом з рештою ших тій. Після розплавлення шихти на поверхню металу загру жають жужільну суміш. Основне призначення шлаку при індук ционной плавці - зменшити теплові втрати металу, захисту тить його від насичення газами, зменшити угар легуючих елементів. При плавці в кислому печі після розплавлення і видалений ня плавильного шлаку наводять шлак з бою скла (SiO2). Метал раскисляют феросиліцію, феромарганцю і алюмінієм перед випуском його з печі. Тривалість плавки в індукційної печі ємністю 1 т близько 45 хв. Витрата електроенергії на 1 т сталі складає 600 ... 700 кВт.год
Вакуумна плавка в індукційних пе чах дозволяє отримувати сталь і сплави з дуже малим утримуючи ням газів, неметалевих включень, легувати сталь і сплави будь-якими елементами. При вакуумної індукційної плавки індуктор з тиглем, дозатор шихти і виливниці поміщають в ва-куумние камери. Тут плавлять метал, вводять легуючі до добавки, раскислители за допомогою спеціальних механізмів без порушення вакууму в камері. Метал в виливниці розливають у вакуумі або інертних газах під надлишковим тиском. Заливку під тиском інертного газу виробляють для підвищення пліт ності злитків.
|