КАТЕГОРИИ:
АстрономияБиологияГеографияДругие языкиДругоеИнформатикаИсторияКультураЛитератураЛогикаМатематикаМедицинаМеханикаОбразованиеОхрана трудаПедагогикаПолитикаПравоПсихологияРиторикаСоциологияСпортСтроительствоТехнологияФизикаФилософияФинансыХимияЧерчениеЭкологияЭкономикаЭлектроника
|
Поверхностные дефекты
Поверхностные дефекты имеют малую толщину и значительные размеры в двух других измерениях. Обычно это места стыка двух ориентированных участков кристаллической решетки. Ими могут быть границы зерен, границы фрагментов внутри зерна, границы блоков внутри фрагментов. Соседние зерна по своему кристаллическому строению имеют неодинаковую пространственную ориентировку решеток. Блоки повернуты друг по отношению к другу на угол от нескольких секунд до нескольких минут, их размер 10–5 см. Фрагменты имеют угол разориентировки не более 5°. Если угловая разориентировка решеток соседних зерен меньше 5°, то такие границы называются малоугловыми границами. Такая граница показана на рис. 1.11. Все субзеренные границы (границы фрагментов и блоков) — малоугловые. Строение границ зерен оказывает большое влияние на свойства металла.
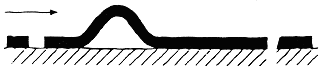
Рис. 1.9.Схема движения дислокации по аналогии с перемещением складки на ковре
|
| Рис. 1.10. Влияние искажений кристаллической решетки на прочность кристаллов
| Рис. 1.11. Схема малоугловой границы между блоками
| На рис. 1.12 показано, что границы зерен и фаз могут совпадать (когерентные), совпадать частично (полукогерентные) и не совпадать (некогерентные).
Граница между зернами представляет собой узкую переходную зону шириной 5–10 атомных расстояний с нарушенным порядком расположения атомов. В граничной зоне кристаллическая решетка одного зерна переходит в решетку другого (рис. 1.13). Неупорядоченное строение переходного слоя усугубляется скоплением в этой зоне дислокаций и повышенной концентрацией примесей.
Плоскости и направления скольжения в соседних зернах не совпадают. Скольжение первоначально развивается в наиболее благоприятно ориентированных зернах. Разная ориентировка систем скольжения не позволяет дислокациям переходить в соседние зерна, и, достигнув границы зерен, они останавливаются. Напряжения от скопления дислокаций у границ одних зерен упруго распространяются через границы в соседние зерна, что приводит в действие источники образования новых дислокаций (источники Франка—Рида). Происходит передача деформации от одних зерен к другим, подобно передаче эстафеты в легкоатлетических соревнованиях.
|
| Рис. 1.12. Схема межфазных границ: а) когерентные; б) полукогерентные; в) некогерентные
| Рис. 1.13. Схема строения зерен и границ между ними
| Вследствие того, что границы зерен препятствуют перемещению дислокаций и являются местом повышенной концентрации примесей, они оказывают существенное влияние на механические свойства металла.
Под размером зерна принято понимать величину его среднего диаметра, выявляемого в поперечном сечении. Это определение условно, так как действительная форма зерна в металлах меняется в широких пределах — от нескольких микрометров до миллиметров. Размер зерна оценивается в баллах по специальной стандартизованной шкале и характеризуется числом зерен, приходящихся на 1 мм2 поверхности шлифа при увеличении в 100 раз (рис. 1.14).
Процесс пластического течения, а, следовательно, и предел текучести зависят от длины свободного пробега дислокаций до «непрозрачного» барьера, т. е. до границ зерен металла. Предел текучести sТ связан с размером зерна d уравнением Холла—Петча: sТ = sо + kd–1/2, где sо и k — постоянные для данного металла. Чем мельче зерно, тем выше предел текучести и прочность металла. Одновременно при измельчении зерна увеличиваются пластичность и вязкость металла. Последнее особенно важно для металлических изделий, работающих при низких температурах. Повышенные пластичность и вязкость обусловлены более однородным составом и строением мелкозернистого металла, отсутствием в нем крупных скоплений, структурных несовершенств, способствующих образованию трещин.
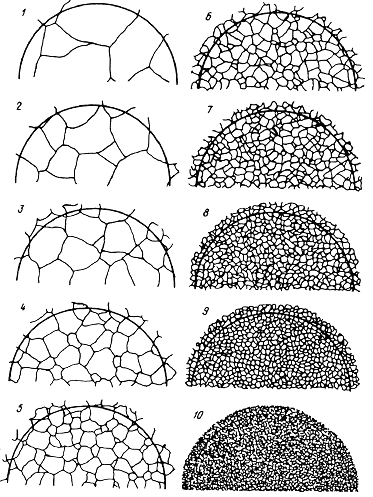
Рис. 1.14. Шкалы для определения величины зерна (ГОСТ 5639-82)
Рост зерен аустенита эффективно затрудняет дисперсные частицы второй фазы — карбидов, нитридов, неметаллических включений. Частицы нитрида AlN, содержащиеся в спокойных сталях, раскисленных алюминием, препятствуют росту аустенитных зерен.
В легированных сталях рост зерен аустенита тормозится карбидами и карбонитридами легирующих элементов V, Ti, Nb, микродобавки которых в количестве около 0,1 % специально вводят в стали с целью сохранения мелкого зерна аустенита вплоть до 1000 °С. Использование этих элементов одновременно обеспечивает мелкозернистую структуру и снижение критической температуры хрупкости.
Помимо перечисленных дефектов в металле имеются макродефекты объемного характера: поры, газовые пузыри, неметаллические включения, микротрещины и т. д. Эти дефекты снижают прочность металла.
1.2. Механические свойства
Поведение металлов под действием внешних нагрузок характеризуется их механическими свойствами, которые позволяют определить пределы нагрузки для каждого конкретного материала, произвести сопоставимую оценку различных материалов и осуществить контроль качества металла в заводских и лабораторных условиях.
К испытаниям механических свойств предъявляется ряд требований. Температурно-силовые условия проведения испытаний должны быть по возможности приближены к служебным условиям работы материалов в реальных машинах и конструкциях. Вместе с тем методы испытаний должны быть достаточно простыми и пригодными для массового контроля качества металлургической продукции. Поскольку необходимо иметь возможность сопоставления качества разных конструкционных материалов, методы испытаний механических свойств должны быть строго регламентированы стандартами.
Результаты определения механических свойств используют в расчетной конструкторской практике при проектировании машин и конструкций. Наибольшее распространение имеют следующие виды механических испытаний.
1. Статические кратковременные испытания одно-кратным нагружением на одноосное растяжение - сжатие, твердость, изгиб и кручение.
2. Динамические испытания с определением ударной вязкости и ее составляющих - удельной работы зарождения и развития трещины.
3. Испытания переменной нагрузкой с определением предела выносливости материала.
4. Испытания на термическую усталость. Испытания на ползучесть и длительную прочность.
5. Испытания на сопротивление развитию трещины с определением параметров вязкости разрушения.
7.Испытания материалов в условиях сложнонап-ряженного состояния, а также натурные испытания деталей, узлов и готовых конструкций.
а б
Рис. 1.1. Схема машинных диаграмм растяжения пластичных материалов: а – с площадкой текучести, б – без площадки текучести
Наиболее часто проводят испытания на растяжение (ГОСТ 1497-84). Обычно применяют малый пятикратный образец круглого сечения (диаметр 5 мм, расчетная длина 25 мм). На рис. 1.1. приведены два вида диаграмм растяжения: с площадкой и без площадки текучести в координатах нагрузка Р - удлинение ∆ℓ. Диаграмма просто преобразуется в диаграмму в координатах напряжение σ - относительная деформация δ. При этом σ = P/F0; δ = (∆ℓ/ℓ0) ∙ 100 %, где Fo, ℓ0 - начальная площадка сечения и длина образца до испытания.
Диаграмма растяжения состоит из трех участков: упругой деформации ОА, равномерной пластической деформации АВ и сосредоточенной деформации шейки ВС.
В области упругой деформации (участок ОА) зависи-мость между нагрузкой Р и абсолютным упругим удлинением образца ∆ℓ пропорциональна и известна под названием закона Гука:
Р = k∙∆ℓ,
где k = E∙F/ℓ - коэффициент, зависящий от геометрии образца (площади поперечного сечения Fo и длины ℓ0) и свойств ма-териала (параметр Е).
Параметр Е (МПа) называют модулем нормальной упругости, характеризующим жесткость материала, которая связана с силами межатомного взаимодействия. Чем выше Е, тем материал жестче и тем меньшую упругую деформацию вызывает одна и та же нагрузка. Закон Гука чаще представляют в следующем виде:
σ = Е∙δ,
где σ = P/Fo - нормальное напряжение; δ = ∆ℓ/ℓо - относительная упругая деформация.
При растяжении определяют следующие показатели прочности и пластичности материалов.
Показатели прочности материалов характеризуются удельной величиной - напряжением, равным отношению нагрузки в характерных точках диаграммы растяжения к площади поперечного сечения образца. Дадим определение наиболее часто используемым показателям прочности материалов.
Предел текучести (физический) (σт, МПа) - это наименьшее напряжение, при котором материал деформируется (течет) без заметного изменения нагрузки:
σт = Рт / F 0 ,
где Рт - нагрузка, соответствующая площадке текучести на диаграмме растяжения (см. рис. 1.1, а).
Если на машинной диаграмме растяжения нет площадки текучести (см. рис. 1.1, б), то задаются допуском на остаточную деформацию образца и определяют условный предел текучести.
Условный предел текучести (σ0,2, МПа) - это напряжение, при котором остаточное удлинение достигает 0,2% от начальной расчетной длины образца:
σ0,2 = Р0,2 / F0 ,
где Р0,2 - нагрузка, соответствующая остаточному удлинению ∆ℓ0,2 = 0,002 ∙ℓ0.
Временное сопротивление (предел прочности) (σв, МПа) - это напряжение, соответствующее наибольшей нагрузке Рmax, предшествующей разрыву образца:
σв = Pmax / F0 .
Истинное сопротивление разрыву ( Sк, МПа) - это напряжение, определяемое отношением нагрузки Рк в момент разрыва к площади поперечного сечения образца в месте разрыва Fk:
Sк = Pк / Fк ,
где Fк = nd / 4.
Пластичность - одно из важных механических свойств металла, которое в сочетании с высокой прочностью делает его основным конструкционным материалом. Дадим определение наиболее часто используемым показателям пластичности материалов.
Предельное равномерное удлинение (δр, %) - это наибольшее удлинение, до которого образец деформируется равномерно по всей его расчетной длине, или, другими словами, это отношение абсолютного приращения расчетной длины образца ∆ℓр до нагрузки Рmax к ее первоначальной длине (см. рис. 1.1, а):
δр = ( ∆ℓр/ ℓ0)∙ 100 = [(ℓp- ℓ0)/ ℓ0 ] ∙100.
Аналогично предельному равномерному удлинению существует предельное равномерное сужение (ψр,%):
ψp = (∆Fр / F0)∙ 100 = [(F0 - Fp) / F0]∙ 100,
где Fр = nd /4 - площадь поперечного сечения образца, соответствующая Рmax. Из условия постоянства объема образца при растяжении можно получить
ψр = δp / (l + δp).
При разрушении образца на две части определяют конечные показатели пластичности: относительное удлинение и относительное сужение образца после разрыва.
Относительное удлинение после разрыва (δ,%) - это отношение приращения расчетной длины образца после разрыва ∆ℓк к ее первоначальной длине:
δ = (∆ℓк / ℓ0)∙100 = [(ℓк - ℓ0) / ℓ0]∙100.
Относительное удлинение после разрыва зависит от соотношения ℓ0 и Fo, т. е. от кратности образцов. Чем меньше отношение ℓ0 / и кратность образца, тем больше δ. Это объясняется влиянием шейки образца, где имеет место сосредоточенное удлинение. Поэтому индекс у δ указывает на кратность образца, например δ2,5 , δ5, δ10 .
Относительное сужение после разрыва (ψ,%) - это отношение уменьшения площади поперечного сечения образца в месте разрыва ∆Fк к начальной площади поперечного сечения:
ψ = (∆Fк / F0)∙ 100 = [(Fo – Fк) / F0]∙ 100.
В отличие от конечного относительного удлинения конечное относительное сужение не зависит от соотношения ℓ0 и Fo (кратности образца), так как в последнем случае дефор-мацию оценивают в одном, наиболее узком, сечении образца.
Условно принято считать металл надежным при δ ≥ 15%, ψ ≥ 45%.
Наиболее простым методом испытания свойств является измерение твердости. Твердостью называют свойство материала оказывать сопротивление деформации в поверхностном слое при местных контактных воздействиях. Наибольшее примене-ние получило измерение твердости вдавливанием. В результате вдавливания достаточно большой нагрузкой поверхностные слои металла, находящиеся под наконечником и вблизи него, пластически деформируются. После снятия нагрузки остается отпечаток. Особенность происходящей при этом деформации заключается в том, что она протекает только в небольшом объеме, окруженном недеформированным металлом. В таких условиях испытания, близких к всестороннему неравномерному сжатию, возникают главным образом касательные напряжения, а доля растягивающих напряжений незначительна по сравнению с получаемыми при других видах механических испытаний (на растяжение, изгиб, кручение, сжатие). При измерении твердости вдавливанием пластическую деформацию испытывают не только пластичные сплавы, но и металлы (например, чугун), которые при обычных механических испытаниях (на растяжение, сжатие, кручение, изгиб) разрушаются хрупко почти без макроскопически заметной пластической деформации.
Таким образом, твердость характеризует сопротивление пластической деформации и представляет собой механическое свойство металла, отличающееся от других его механических свойств способом измерения. Я. Б. Фридман предложил рассматривать измерения твердости как «местные механические испытания поверхностных слоев материала». Преимущества измерения твердости следующие:
1. Между твердостью пластичных металлов, определя-емой способом вдавливания, и другими механическими свойствами (главным образом временным сопротивлением), существует количественная зависимость. Величина твердости характеризует временное сопротивление металлов, получающих в испытаниях на растяжение сосредоточенную пластическую деформацию (шейку), а именно сталей (кроме сталей с аустенитной и мартенситной структурой) и многих цветных сплавов. Это связано с тем, что при испытаниях на растяжение наибольшей нагрузке, предшествующей разрушению и отнесенной к его первоначальной площади (временное сопротивление), отвечает сосредоточенная пластическая деформация (образование шейки), а не разрушение образца. Такая пластическая деформация аналогична деформации, создаваемой в поверхностных слоях металла при измерении твердости вдавливанием наконечника.
Подобная количественная зависимость не наблюдается для хрупких материалов, которые при испытаниях на растяжение (или сжатие, изгиб, кручение) разрушаются без заметной пластической деформации, а при измерении твердости получают пластическую деформацию. Однако в ряде случаев и для этих металлов (например, серых чугунов) наблюдается качественная зависимость между пределом прочности и твердостью; возрастанию твердости обычно соответствует увеличение предела прочности на сжатие. По значениям твердости можно определять также и некоторые пластические свойства металлов. Твердость, определенная вдавливанием, характеризует также предел выносливости некоторых металлов, в частности меди, дуралюмина и сталей в отожженном состоянии.
Измерение твердости по технике выполнения значительно проще, чем определение прочности, пластич-ности и вязкости. Испытание твердости не требует изготовления специальных образцов и выполняется непосредственно на проверяемых деталях после зачистки на поверхности ровной горизонтальной площадки, а иногда даже и без такой подготовки. Измерение твердости выполняется быстро, например, при вдавливании конуса за 30 - 60 с, а при вдав-ливании шарика за 1-3 мин.
Измерение твердости обычно не влечет за собой разрушения проверяемой детали, и после измерения ее можно использовать по своему назначению, в то время как для определения прочности, пластичности и вязкости необходимо изготовление специальных образцов из детали.
Твердость можно измерять на деталях небольшой толщины, также в очень тонких слоях, не превышающих (для некоторых способов измерения твердости) десятых долей миллиметра или в микрообъемах металла; в последнем случае измерения проводят способом микротвердости.
Многие способы измерения твердости пригодны для оценки различных по структуре и свойствам слоев металла, например поверхностного слоя цементованной, азотированной или закаленной стали, имеющей разную твердость по сечению детали. Методом определения микротвердости можно измерять также твердость отдельных составляющих в сплавах. Для полной характеристики свойств металла необходимо наряду с измерением твердости проводить остальные механические испытания. Поскольку при измерении твердости в большинстве случаев детали не разрушаются, то эти измерения можно применять для сплошного контроля деталей, в то время как определение характеристик прочности и пластичности проводят в качестве выборочного контроля.
Измерение твердости (макротвердости) характеризуется тем, что в испытуемый материал вдавливается тело, проникающее на сравнительно большую глубину, зависящую прежде всего от величины прилагаемой нагрузки и свойств металла. Кроме того, во многих испытаниях вдавливается тело значительных размеров, например стальной шарик диаметром до 10 мм, в результате чего в деформируемом объеме ока-зываются представленными все фазы и структурные составляющие сплава в количествах и с расположением, характерными для измеряемого материала. Измеренная твердость должна в этом случае характеризовать твердость всего испытуемого материала.
Выбор формы, размеров наконечника и величины нагрузки зависят от целей испытания структуры, ожидаемых свойств, состояния поверхности и размеров испытуемого образца. Если металл имеет гетерогенную структуру с крупными выделениями отдельных структурных составляющих, различных по свойствам (например, серый чугун, цветные подшипниковые сплавы), то для испытания твердости следует выбирать шарик большого диаметра. Если же металл имеет сравнительно мелкую и однородную структуру, то малые по объему участки испытуемого металла могут быть достаточно характерными для оценки свойств материала в целом и, в частности, его твердости. В этих случаях испытания можно проводить вдавливанием тела меньшего размера, например алмазного конуса или пирамиды, и на меньшую глубину, и, следовательно, при небольшой нагрузке.
При испытании металлов с высокой твердостью, например закаленной или низкоотпущенной стали, приведенное условие является даже обязательным, поскольку вдавливание стального шарика или алмаза с большой нагрузкой может вызывать деформацию шарика или скалывание алмаза. Однако значительное снижение нагрузки нежелательно, так как это приведет к резкому уменьшению деформируемого объема и может дать значения, не характерные для основной массы металла. Нагрузки и размеры получаемых в материалах отпечатков не должны быть меньше определенных пределов.
У полимерных материалов измерение твердости дает меньше информации об их свойствах, так как между твердостью и прочностью этих материалов нет определенной зависимости. Результаты измерений являются лишь дополнительной характеристикой свойств полимерных материалов.
Значительное влияние на результаты испытаний твердости оказывает состояние поверхности измеряемого материала. Если поверхность неровная (криволинейная или с выступами), то отдельные участки в различной степени участвуют в сопротивлении вдавливанию и деформации, что приводит к ошибкам в измерении. Чем меньше нагрузка для вдавливания, тем более тщательно должна быть подготовлена поверхность. Она должна представлять шлифованную горизонтальную площадку.
Измеряемая поверхность должна быть установлена горизонтально, т. е. перпендикулярно действию вдавливаемого тела. Противоположная сторона образца также должна быть зачищена и не иметь окалины, так как последняя при нагружении образца сминается, что искажает результаты измерения.
Различают следующие методы определения твердости: по Бринеллю (по диаметру отпечатка шарика); по Роквеллу (по глубине вдавливания алмазного конуса или закаленного шари-ка); по Виккерсу (для деталей малой толщины или тонких по-верхностных слоев твердость определяют по диагонали отпе-чатка алмазной пирамиды). Схемы этих методов приведены на рис. 1.2. При испытании на твердость по методу Бринелля (ГОСТ 9012-59) в поверхность материала вдавливается твердо-сплавный шарик диаметром D под действием нагрузки Р и после снятия нагрузки измеряется диаметр отпечатка d (рис. 1.2, а). Число твердости по Бринеллю (НВ) подсчитывается как отношение нагрузки Р к площади поверхности сферического отпечатка М:
HB = = .
Метод Бринелля не рекомендуется применять для материалов с твердостью более 450 HB, так как стальной шарик может заметно деформироваться, что внесет погрешность в результаты испытаний.
Временное сопротивление и число твердости по Бринел-лю связаны между собой: для стали σв = 0,34 HB, для медных сплавов σв = 0,45 HB, для алюминиевых сплавов σв = 0,35 HB.
а
Рис. 1.2. Схема определения твердости: а – по Бринеллю; б – по Роквеллу
При испытании на твердость по методу Роквелла (ГОСТ 9013-59) в поверхность материала вдавливается алмазный конус с углом при вершине 120° или стальной шарик диаметром 1,588 мм. Однако, согласно этому методу, за условную меру твер-дости принимается глубина отпечатка. Схема испытания по методу Роквелла показана на рис. 1.2, б. Вначале прикладыва-ется предварительная нагрузка Р0, под действием которой индентор вдавливается на глубину h0. Затем прикладывается основная нагрузка Р1 под действием которой индентор вдавливается на глубину h. После этого снимают нагрузку Р1, но оставляют предварительную нагрузку Р0 . При этом под действием упругой деформации индентор поднимается вверх, но не достигает уровня h0. Разность (h - h0) зависит от твердости материала; чем тверже материал, тем меньше эта разность.
Глубина отпечатка измеряется индикатором часового типа с ценой деления 0,002 мм. При испытании мягких металлов методом Роквелла в качестве индентора применяется стальной шарик. Последовательность операций такая же, как и при испытании алмазным конусом. Число твердости, определенное методом Роквелла, обозначается символом HR. Однако в зависимости от формы индентора и значений нагрузок вдавливания к этому символу добавляется буква А, или С, или В, обозначающая соответствующую шкалу измерений. Обозначения твердости и значения нагрузок вдавливания для разных шкал измерений методом Роквелла приведены ниже:
Шкала................. А С В
Индентор........... Алмазный Алмазный Стальной
конус конус шарик
Обозначение
твердости HRA HRC HRB
Нагрузи вдавливания,
кгс (Н): Ро 10(98,1) 10(98,1) 10(98,1)
P1 50(490,5) 140(1373,4) 90(882,9)
Р 60(588,6) 150(1471,5) 100(981)
Различие в нагрузке Р1 для шкал А и С объясняется тем, что по шкале А измеряют твердость особо твердых материалов и в этом случае во избежание повреждений алмазного конуса рекомендуется меньшая нагрузка вдавливания.
Для оценки склонности материалов к хрупкому разрушению широко применяют испытания на ударный изгиб образцов с надрезом, в результате которых определяют ударную вязкость. Ударная вязкость оценивается работой, затраченной на ударный излом образца и отнесенной к площади его поперечного сечения в месте надреза.

а б

в
Рис. 1.3. Образцы для испытаний на ударную вязкость: а - с U-образным надрезом; б – с V-образным надрезом; в – с Т-образным надрезом
Согласно ГОСТ 9454-78, для определения ударной вязкости применяют призматические образцы с надрезами различных типов. Самыми распространенными типами являются образцы с U-образным (рис. 1.3, а) , V-образным (рис. 1.3, б) и Т-образным (инициированная трещина) надрезами (рис.1.3, в)
Испытания на ударную вязкость проводят на маятниковом копре. Схема испытаний приведена на рис. 1.4.
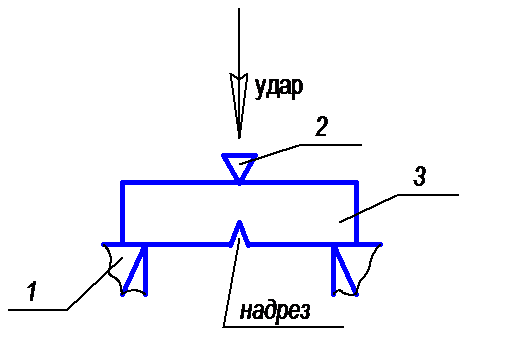
Рис. 1.4. Схема испытаний на ударную вязкость: 1 – корпус; 2 – маятник; 3 – образец
Ударная вязкость КС, Дж/см2, определяется как отношение работы разрушения К, затраченной на деформацию и разрушение ударным изгибом надрезанного образца, к начальной площади поперечного течения образца в месте надреза So по формуле:
КС = K / S0.
Ударная вязкость обозначается символом КС, МДж / м2 Если образец с U-образным надрезом, то к символу добавляется буква U (KCU), если с V-образным надрезом, то добавляется буква V (KCV), если с Т-образным надрезом, то добавляется буква Т (KCT).
Обычно снижение ударной вязкости ниже 40 Дж / м2 (3-4 ) значительно увеличивает опасность хрупкого разру-шения, поэтому одним из условий надежной работы материала является значение ударной вязкости KCU≥ 50 Дж /м2.
Хладноломкостью называют способность некоторых металлов охрупчиваться при низких температурах. К хладно-ломким металлам можно отнести металлы с решеткой объемно-центрированного куба, например Fea, и гексагональной, напри-мер Zn. Для этой группы металлов при определенной минусовой температуре наблюдается резкое снижение ударной вязкости.
К нехладноломким металлам можно отнести металлы с решеткой гранецентрированного куба, например Fer, Al, Ni и др.
Деление металлов на хладноломкие и нехладноломкие является условным, так как, например, аустенитные стали, име-ющие решетку гранецентрированного куба, тоже подвержены охрупчиванию, но только в меньшей степени и при более низких температурах, чем углеродистые и низколегированные стали, имеющие решетку объемноцентрированного куба.
Испытания на ударную вязкость при низких темпера-турах позволяют получить хрупкое разрушение металла в ре-зультате одновременного действия надреза, повышенной ско-рости деформирования и температуры. |
|